What is Porosity in Welding: Necessary Tips for Achieving Flawless Welds
Unraveling the Mystery of Porosity in Welding: Tips for Lessening Issues and Making The Most Of Quality
In the detailed globe of welding, porosity stays a consistent difficulty that can dramatically influence the top quality and honesty of bonded joints. As we delve into the depths of porosity in welding, revealing the secrets to its avoidance and control will certainly be paramount for professionals looking for to master the art of top notch weldments.
Comprehending Porosity in Welding
Porosity in welding, a common concern run into by welders, refers to the visibility of gas pockets or gaps in the bonded material, which can compromise the integrity and top quality of the weld. These gas pockets are normally entraped throughout the welding procedure as a result of various variables such as incorrect shielding gas, contaminated base materials, or inaccurate welding specifications. The development of porosity can damage the weld, making it prone to cracking and corrosion, inevitably causing structural failings.
By recognizing the relevance of keeping correct gas shielding, guaranteeing the cleanliness of base materials, and maximizing welding setups, welders can dramatically minimize the likelihood of porosity formation. Overall, an extensive understanding of porosity in welding is essential for welders to produce high-quality and resilient welds.
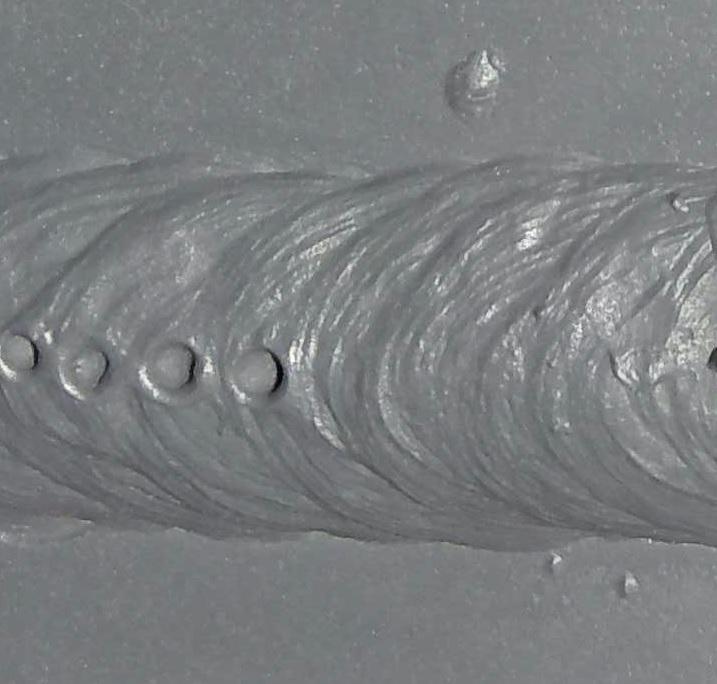
Usual Sources Of Porosity
When evaluating welding processes for prospective quality concerns, understanding the common reasons for porosity is necessary for keeping weld integrity and preventing structural failings. Porosity, identified by the visibility of dental caries or voids in the weld metal, can dramatically endanger the mechanical properties of a welded joint. One typical reason of porosity is improper shielding gas insurance coverage. Poor shielding gas flow prices or improper gas mixtures can bring about climatic contamination, leading to porosity development.
An additional prevalent source of porosity is the visibility of wetness and pollutants externally of the base steel or filler material. When welding materials are not effectively cleaned up or are exposed to high degrees of moisture, the evaporation of these contaminants during welding can produce gaps within the weld grain. In addition, welding at incorrect parameters, such as exceedingly high travel rates or currents, can generate excessive disturbance in the weld pool, trapping gases and creating porosity. By attending to these common causes with proper gas protecting, product preparation, and adherence to optimum welding specifications, welders can reduce porosity and enhance the quality of their welds.
Strategies for Porosity Avoidance
Applying efficient preventative procedures is vital in minimizing the incident of porosity in welding procedures. One strategy for porosity avoidance is making certain appropriate cleaning of the base steel before welding. Pollutants such as oil, oil, corrosion, and paint can cause porosity, so extensive cleansing using suitable solvents or mechanical approaches is crucial.

Another secret safety net is the selection of the appropriate welding consumables. Making use of high-quality filler products and securing gases that appropriate for the base steel and welding process can substantially lower the threat of porosity. Furthermore, keeping appropriate welding criteria, such as voltage, current, travel rate, and gas circulation rate, is important for porosity avoidance. Differing the advised setups can lead to improper gas protection and inadequate combination, leading to porosity.
In addition, using correct welding techniques, such as preserving a regular traveling speed, electrode angle, and arc length, can aid prevent porosity (What is Porosity). Appropriate training of welders to ensure they follow ideal techniques and quality assurance treatments is likewise crucial in minimizing porosity flaws in welding
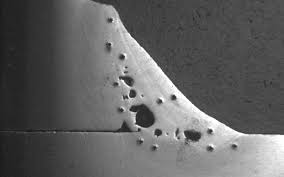
Ideal Practices for Quality Welds
Guaranteeing adherence to industry criteria and proper weld joint preparation are fundamental elements of attaining continually top quality welds. In enhancement to these fundamental steps, there are a number of ideal practices that welders can implement to even more boost the high quality of their welds. One key practice is preserving proper cleanliness in the welding location. Contaminants such as oil, grease, corrosion, and paint can negatively influence the top quality of the weld, leading to issues. Extensively cleaning the workpiece and bordering area before welding can help minimize these issues.
One more best method is to meticulously select the appropriate welding specifications for the certain materials being Click This Link joined. Correct specification option ensures optimal weld penetration, combination, and overall quality. Making use of top notch welding consumables, such as electrodes and filler metals, can considerably affect the last weld high quality.
Relevance of Porosity Control
Porosity control plays an important role in guaranteeing the stability and high quality of welding joints. Porosity, defined by the visibility of cavities or voids within the weld metal, can dramatically jeopardize the mechanical residential properties and structural integrity of the weld. Extreme porosity weakens the weld, making it more vulnerable to splitting, deterioration, and general failing under operational tons.
Effective porosity control is important for preserving the preferred mechanical homes, such as strength, ductility, and sturdiness, of the welded joint. What is Porosity. By lessening porosity, welders can improve the overall top quality and dependability of the weld, making certain that it fulfills the efficiency needs of the intended application
In addition, porosity control is vital for attaining the desired aesthetic look of the weld. Excessive porosity not just deteriorates the weld however also takes away from its visual charm, which can be essential in industries where aesthetics are necessary. Appropriate porosity control strategies, such as using the right securing gas, pop over to these guys regulating the welding specifications, and guaranteeing proper sanitation of the base materials, are vital for browse around this site producing high-quality welds with minimal flaws.
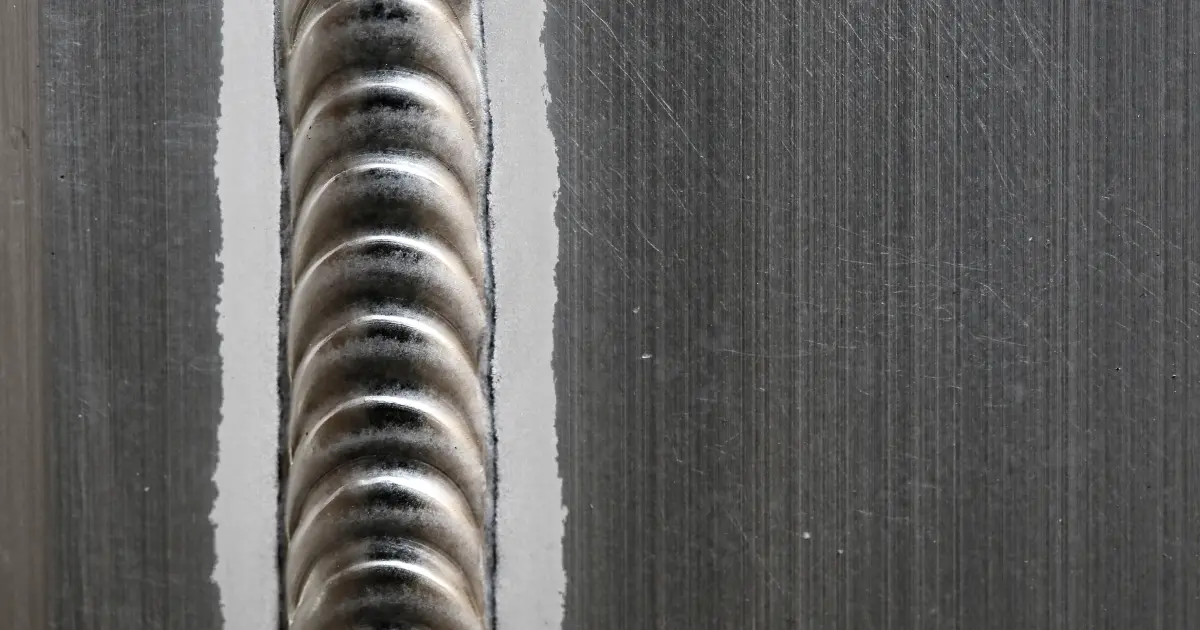
Conclusion
To conclude, porosity in welding is an usual defect that can compromise the top quality of the weld. By comprehending the root causes of porosity and applying appropriate avoidance strategies, welders can lessen flaws and achieve greater top quality welds. It is important to regulate porosity in welding to ensure the honesty and toughness of the final item. Executing finest methods for porosity control is critical for achieving optimum welding results.